Got the door almost ready for another coat. As you can see in the pictures we use an iron sander to hit the spots that get runs and the varnish collects. Then the rest of the door gets the red scratch pad treatment.
We are currently cruising our Islander Freeport 36 sailboat in Mexico. We have been extensively documenting our outfitting for this adventure. Also, what works and what is not of value.
Insulation - foaming meltdown
We cleaned the refer again removing any loose partials and Debbie tapped brown all over the area. She also picked up some more blue through away gloves. We had gotten some at Ace Hardware but they were clear and crap so we got some good ones.
Debbie did the leveling and I did the spraying. It does not look level but that is because the foam expanded. Debbie worked hard at getting the foam into the crevices where the Dow Blue Board (DBB) had melted. We used almost a whole can of spray foam.
The leftover we used in the freezer.
I tried to fill the old spill over (it is covered now by foam on the refer side) but it will be better done with DBB.
Cleaned it up some but it was still expanding
Now we will need to sand it. It will take a day or so to set up good.
JD's florescent lights
JD had a few low profile florescent lights up for grabs that he took off his boat as he replaced his with LED strips on his Islander Freeport.
We grabbed them because one of ours is broken. Also one shade is broken. He was nice enough to give them to us free of charge! They are not made any more that I know of.
There are five of them in the salon. There is one over the nav station and two on each side of the boat.
We plan on converting them into LED’s later on, keeping the fixture and adding LED strips inside. It is a project we do not have time for right now.
Epoxy the refer - how too
Well, went to Fiberlay and talked to Kevin and he is the man. Speak to no one else there or you will be disappointed.
Any way Kevin told me how to make a fiber glass sheet.
Using a piece of Plexiglas you wax it with some car wax or other wax. Then using the epoxy and fiber glass cloth make the sheet on top of the Plexiglas. Then take the cloth he gave me and lay it over the fiber glass. Squeegee it out with a rubber squeegee like shown below and let it dry. The cloth will come off and the fiber glass will come off the Plexiglas. There you have it!
Kevin also said if we had epoxied the foam first the resin filler would have not reacted with the foam. Oh well.
So I got some “bobbles” which are used as filler to make a paste to be used for the corners and making radios.
So first we sand everything in the refer down with #80 grit.
Then measure all the flat areas and make fiber glass pieces for them.
Then fiber glass in each piece using the epoxy.
Then put in the epoxy filler made with the bobbles into all the corners and edges to make them radiouses.
You put it into a Ziploc bag and squeeze it into a corner of the bag. Then get all the air out of the bag and cut the corner off the bag. Now it can be squeezed into the corners and squeegeed to perfection.
Now using fiber glass tape you fold it in half and place it into the edges and then wet it out with epoxy.
Now you use some heavier fiber glass cloth and put another layer on the bottom.
You can use the lighter cloth on the side s for a second layer after the tape has been installed.
Using push pins if needed to hold the cloth in lace.
So let’s see how this all works out :)
Evaporator plate Ordered
OK just ordered the Frigoboat Evaporator 200F Flat for the freezer from Swedish Marine.
We need the Evaporator plate to get a better idea of how to build out the freezer.
We will need to drill a 1 inch hole through behind the Evaporator 2/3 of the way up the freezer for the fan (taking into consideration the solid middle part of the fan.) Then drill a 1 inch hole up as high as possible behind the Evaporator for the return into the freezer for hot air. The hole for the fan can not be too big or it will freeze to contents of the refer :) This all has to be done after it is all put together except for the Evaporator plate, it will go in last.
We need the Evaporator plate to get a better idea of how to build out the freezer.
We will need to drill a 1 inch hole through behind the Evaporator 2/3 of the way up the freezer for the fan (taking into consideration the solid middle part of the fan.) Then drill a 1 inch hole up as high as possible behind the Evaporator for the return into the freezer for hot air. The hole for the fan can not be too big or it will freeze to contents of the refer :) This all has to be done after it is all put together except for the Evaporator plate, it will go in last.
We are on our way for more excitement!
Swedish Marine
1150 Brickyard Cove Rd. Suite B6
Point Richmond, CA 94801
Phone: 510-234-9566
Toll Free: 877-234-9501
Fax: 510-234-9599
1150 Brickyard Cove Rd. Suite B6
Point Richmond, CA 94801
Phone: 510-234-9566
Toll Free: 877-234-9501
Fax: 510-234-9599
Insulation gluing
We did get a few more pieces of foam put into the refer side. Now there are just two more pieces left. We could not add them as the clamps were in the way from the pieces we did add.
Salon Settee cushions dropped off
We dropped off the foam and cushions at Knox Upholstery.
How exciting!
We are asking them to make the mounting screw holes better so they do not tear up the fabric like the original ones do.
The settee fabric is supposedly already delivered there.
Now the couch is not ours :)
Dow Blew board melt down, NO! - 2011
March 2011 - At Marina Cortez Harbor Island, San Diego, CA
At Fiberlay in San Diego with my 91 Jeep Wrangler parked out front.
Insulation - freezer
We started the freezer side of the refer by cleaning it out and sanding it with the iron sander #80 grit.
The we cleaned with Acetone and glued in our first piece of Dow Blue Board.
Evaporator plate R and D - 2011
March 2011 - At Marina Cortez, San Diego, CA
So we talked to Swedish Marine for tech support on the 200f evaporator plate (40 inches long) and we can make several bends to have it conform to our box.
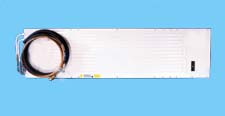
Insulation - foaming
After we spray foamed all the voids in the Dow Blue Board foam we needed to clean it up.
To do this we used a knife to trim off as much as we could and then used the iron sander and #80 grit to sand the foam. This worked well. If you try to pry it off the foam will take out chunks of blue board foam with it.
To do this we used a knife to trim off as much as we could and then used the iron sander and #80 grit to sand the foam. This worked well. If you try to pry it off the foam will take out chunks of blue board foam with it.
Trimming off excess with knife
All sanded
New three blade prop now working on s\v Elegant'sea - 2011
Old two blade prop
The new three blade prop is now on the boat. The old two blade prop was not correct for our engine, atleast without machining. We wanted a three blade prop for cruising.
Salon Settee fabric
We finally decided on a fabric for the salon and the settee!
Yes, we decided on the lighter of the two choices we had come down too.
We tried it at the boat and we liked the it!
It blends with the headline well
Settee fabric
Next to original cushion
It blends with the headline well
It blends with the headline well
It blends with the headline well
The three fabrics, headliner, salon and settee
We decided on a Foe Leather for the salon. It is half leather and half vinyl. It is advertised as feeling like and looking like leather but wearing like vinyl. It does feel supple and looks nice.
Debbie has ordered it up!
We are purchasing the Foe Leather from:
We are purchasing the Foe Leather from:
KOVI Fabrics
Pattern #: K9737 BISQUE
Quantity: 20.00 yards
Quantity: 20.00 yards
We are having the fabric shipped right to the upholsterer.
Knox Upholstery
(858) 268-3541
7586 Clairemont Mesa Blvd
San Diego, CA 92111
Subscribe to:
Posts (Atom)