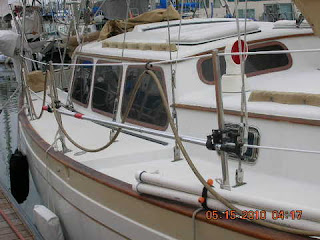
We are currently cruising our Islander Freeport 36 sailboat in Mexico. We have been extensively documenting our outfitting for this adventure. Also, what works and what is not of value.
Boat hook
Because we are in a 35’ slip that is just about wide enough (we use ac couple flat fenders) we decide a boat hook was need to pole out. You can see it mounted on the stanchions. Got to look through the power cord etc. It is a Shroud and we have a bunch of attachments for it. We also have another Shroud pole we use for a broom.
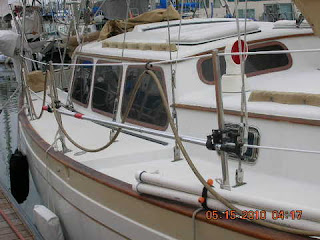
Galvanic Isolator
Head LED red\white light
New dorade (cowl) vent paint
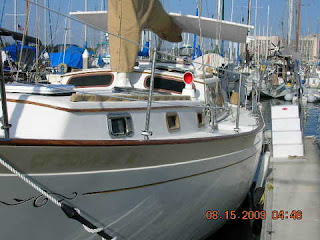
New dorade (cowl) vent paint
An easy and quick project with a big bang. It was simply a matter of washing them real good and removing old paint. I think we used acetone. We then bought some red Rust-Oleum paint from Home Depot and put a couple coats on. They have held up pretty well so far. It’
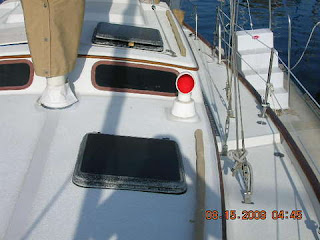
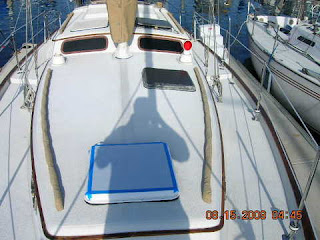
s been at least six months.
Varnishing the vanity in the head or first varnishing project! - 2009
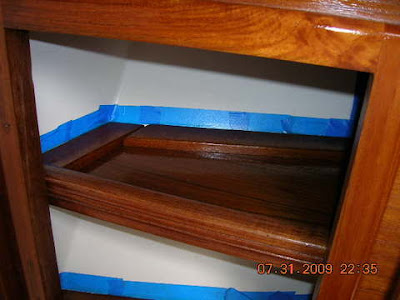
Binnacle engine control project, major project, oh no! - 2009
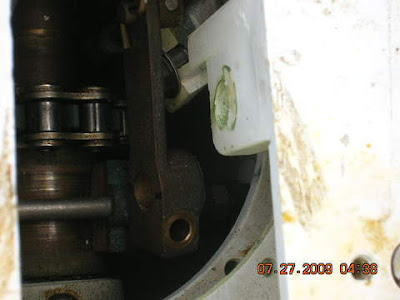
New SHURFLO Extreme Series Smart Sensor Water Pump installed - 2009
2009 - Marina Cortez San Diego, CA
This is the old pump when it was installed. You can see it leaking.
Force 10 stove! installed old stove sold and pot roast made - 2009
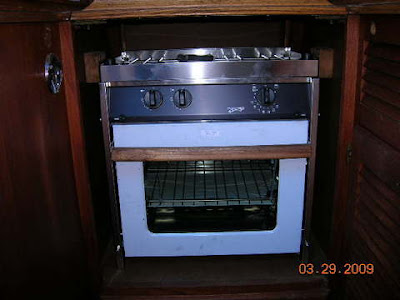
We like it does not need matches to be light.
Alos the oven door folds out of the way.
New Force 10 stove installed and cooked beef stew! - 2009
San Diego 3\29\2009 at Marina Cortez
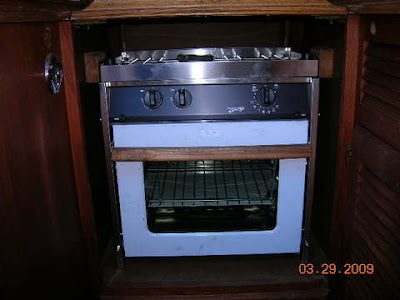
When we bought our boat it had CNG gas stove. Because we will be cursing Mexico and in Mexico they do not have CNG gas readily amiable we decide to switch to propane.
Propane locker build with 2 -10# bottles, plywood - 2009
2009 - Marina Cortez San Diego, CA
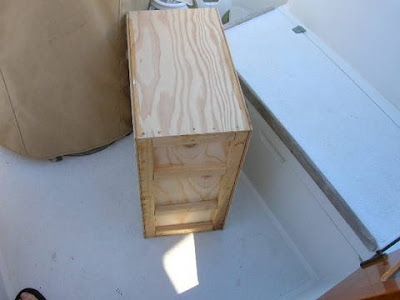
The propane locker took some thought and we decided to put it in the port lazeratt. We decided on two ten pound composite bottles.
New Found Metals Portholes, SS, tinted, teak rings + SS screens - installing - 2009
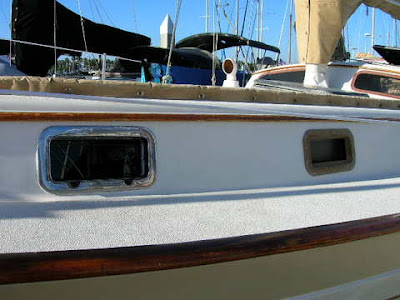
About the time we were finishing the toilet project we started the porthole project.
New Life lines
Subscribe to:
Posts (Atom)